Inconel Machining
Inconel
Inconel alloys are typically used in high temperature applications. Inconel alloys are oxidation and corrosion resistant materials well suited for service in extreme environments. When heated, Inconel forms a thick, stable, passivating oxide layer protecting the surface from further attack. Inconel retains strength over a wide temperature range, attractive for high temperature applications where aluminum and steel would succumb to creep as a result of thermally-induced crystal vacancies
Uses
Inconel is often encountered in extreme environments. It is common in gas turbine blades, seals, and combustors, as well as turbocharger rotors and seals, electric submersible well pump motor shafts, high temperature fasteners, chemical processing and pressure vessels, heat exchanger tubing, steam generators in nuclear pressurized water reactors, natural gas progressing with contaminants, sound suppressor blast baffles, and Formula One exhaust systems. Inconel is increasingly used in the boilers of waste incinerators.
Machining
Inconel is a difficult metal to machine. For this reason, Inconels are machined using an aggressive but slow cut with a hard tool, minimizing the number of passes required. External threads are machined using a lathe to “single point” the threads. Cutting of plate is often done with a waterjet cutter. Internal threads can also be cut by single point method on lathe, or by threadmilling on a machining center.
Inconel alloys
- Inconel 600: Solid solution strengthened
- Inconel 625: Acid resistant, good weldability
- Inconel 690: Low cobalt content for nuclear applications
- Inconel 718: Gamma double prime strengthened with good weldability
CMP, the future of precision manufacturing
When life depends on delivering precision,
You can depend on Chucking Machine Product
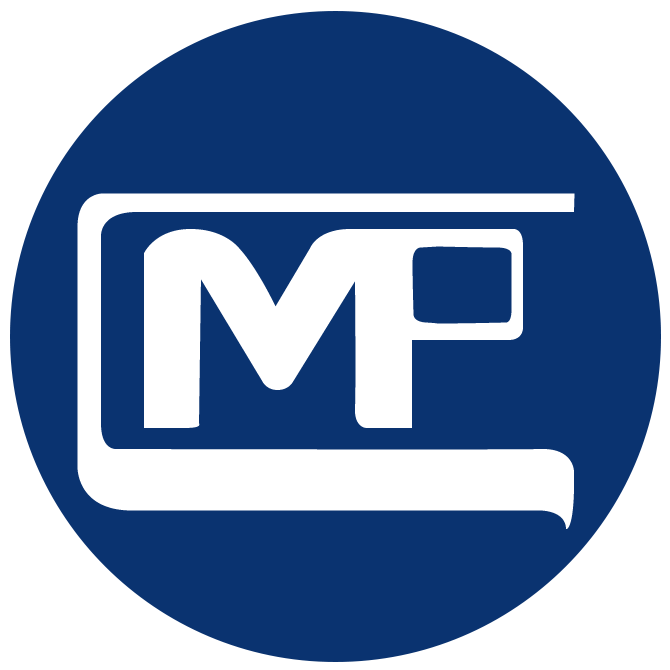