Hastelloy Machining
Hastelloy
A registered trademark name of Haynes International, Inc., Hastelloy is known under a material term as “superalloys” or “high-performance alloys”. Composed of various elements such as molybdenum, chromium, cobalt, iron, copper, manganese, titanium, zirconium, aluminum, carbon and tungsten, Hastelloy is predominantly nickel. Hastelloy machining alloys are known for their corrosion resistance, high-stress corrosion cracking resistance and survival under high-temperatures. They are widely used in moderately to severely corrosive and erosion-prone environments.
Hastelloy Usage
Because Hastelloy machining is corrosion-resistant and high-stress corrosion cracking resistant, it is a widely used alloy in the chemical processing industries, pressure vessels of some nuclear reactors, chemical reactors, distillation equipment and pipes and valves. Hastelloy machining is becoming more widely used in other industries such as energy, health and environmental, oil and gas, pharmaceutical and flue gas desulfurization, aerospace and gas turbines.
Machining Hastelloy
Hastelloy can be machined using conventional methods at satisfactory rates. However, nickel and cobalt base alloys are classified as moderate to difficult when machining. Because these alloys work harden rapidly, generate high heat during cutting and offer high resistance to metal removal, the following Hastelloy machining operation guidelines should be considered:
- To minimize tool overhang, work piece and tool should be held rigid.
- Tools should be sharp at all times and changed at regular intervals.
- Most machining operations require positive rake angle tools. Carbide-tipped tools are suggested for most applications. For intermittent cuts, high-speed tools can be used.
- Machine should be rigid and overpowered as much as possible.
- Minimize tool overhang.
- To maintain positive cutting action, use heavy, constant feeds. Close tolerances are impossible if feed slows or tool dwells in the cut, as work hardening occurs and tool life deteriorates.
- Soluble oils are recommended as lubrication when using carbide tooling.
CMP, the future of precision manufacturing
When life depends on delivering precision,
You can depend on Chucking Machine Products
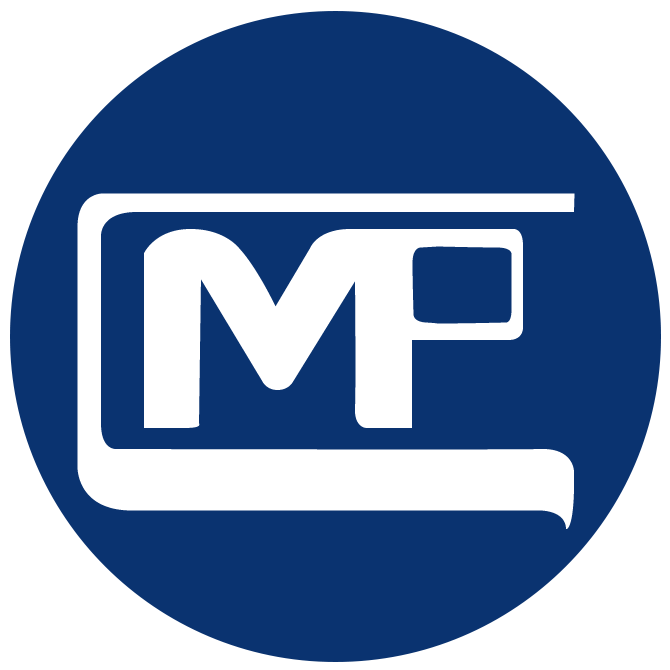